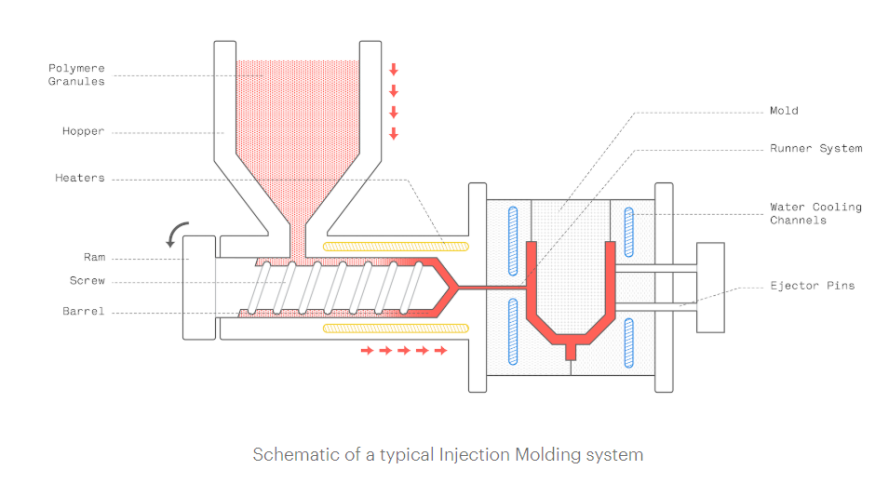
Manufacturing processes like 3D printing and CNC machining are typically used to produce low-volume production batches. When 500 or more units are required, injection molding is almost always the most cost-effective solution. Nearly all plastic objects are made with injection molding; read on to learn about this popular and effective manufacturing method.
Why engineers choose injection molding
Injection molding is a formative manufacturing process that is used to produce very high volumes of identical plastic parts. Although the process has a much higher startup cost than other manufacturing methods, this cost is non-recurring for future production runs. Once an injection mold has been created, it can be stored and re-used for a minimum of two years.
Injection molding is most cost-effective when a minimum of 500 units are produced. Nearly any type of thermoplastic can be used for injection molding, and the finished products are durable and aesthetically pleasing.
Creating injection molds to specifications can take several weeks. However, once the molds have been created, thousands of parts can be produced every hour. For high-volume production, injection molding is one of the most efficient and cost-effective manufacturing options.
For many engineers, the attraction of injection molding is that every part produced is nearly identical. Most molds can be used for up to 10,000 cycles of matching parts; after this point, a new mold is created. If the original mold was made with 3D printing or CNC machining, the new mold should continue to produce identical objects for future production runs.
How does injection molding work?
As the name implies, objects made with injection molding are created by injecting liquid plastic into the cavity of a previously formed mold. Once the plastic has cooled, the item is ejected, and another batch of identical objects can be created using the same mold.
Most injection molds have two readily identifiable parts: the cavity and the core. The core of the mold forms the front or A-side of the object. The cavity is used to form the B-side of the object and may contain ribbing, screw holes, and other structural features. Removable side-action cores can be used to create hollow areas and undercut in the finished object. Cooling channels and ejector pins are frequently included in the mold design.
Injection molds are typically made from aluminum or tool steel. Although injection molds are usually made with CNC machining, 3D printing can be used to quickly produce molds for low-production runs.
Available materials for injection molding
Nearly any type of thermoplastic is compatible with the injection molding process. Thermosets, liquid silicones, and various reinforced blends can also be used. Some of the most common materials are listed below.
ABS: Affordable and popular thermoplastic
Polypropylene: The most commonly used injection molding material
Polyethylene: Lightweight thermoplastic used for outdoor applications
Polystyrene: Extremely affordable but low in durability
Polycarbonate: High impact strength and great thermal resistance
Nylon: Frequently used for engineering applications
PEEK: High-performance plastic often used for medical applications or to replace metal parts
Available surface finishes for injection molding
One of the features that separate injection molding from other manufacturing processes is the ability to achieve unique surface finishes and textures. These finishes do not require post-processing; instead, the finish is incorporated into the design of the original mold.
Glossy: The smoothest possible surface finish
Semi-glossy: Good visual appearance with less reflectivity
Matte: Smooth and without visible machining marks
Textured: Dull, rough, or satin textures are available
As-machined: Machining marks may be visible; not recommended for cosmetic objects